Eagle Maintenance Management
With the EAGLE Maintenance Management Information System (MMIS), inventory management extends beyond simple inventory tracking. Continuous improvement is engrained in this product, and Raytheon has set up several standard practices that infuse inventory management with other disciplines such as integrated logistics support analysis, reliability engineering, and configuration management. They understand that the product life of a system spans decades and monitoring reliability trends and diminishing suppliers is critical if we are going to exceed the operational requirements of your customers. Raytheon has developed a software system that unifies FRACAS, configuration management, preventive maintenance, and inventory management.
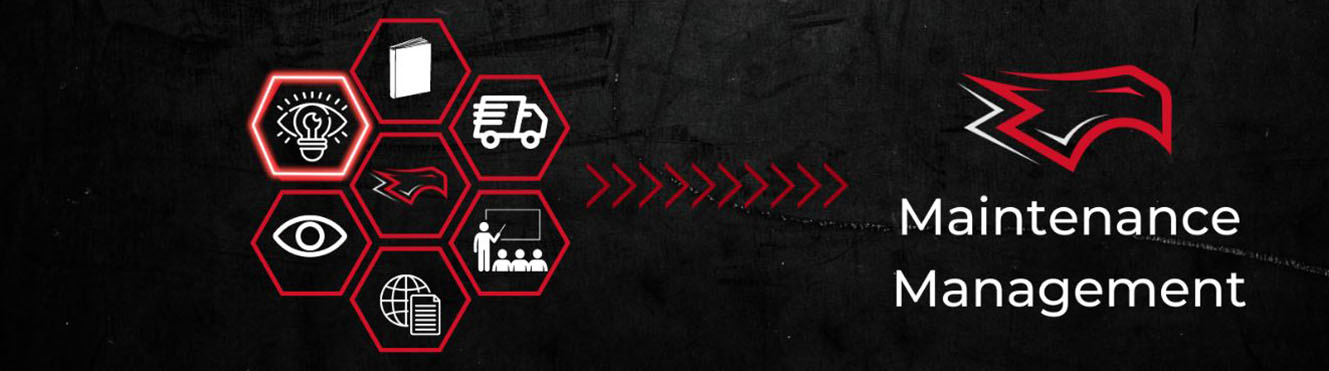
With MMIS, inventory items can be serialized or un-serialized and the configuration of these items can be tracked over time via our MMIS As Maintained Configuration module. Special care is taken to ensure that CAGE Codes, Part Numbers, and National Stock Numbers are controlled and approved by the proper engineering authority. If the contractor chooses, these part numbers can be tracked in S3000L, MIL-STD-1388-2B, or GEIA-STD-0007 repositories to make sure that they conform to standard logistics support analysis practices. Software and firmware configuration can be tracked, and parts can be categories and consumables, test equipment, repairable, and long lead items.
Features:
• Inventory Tracking
o Inventory can be tracked geographically to the site/location/shelf and bin level and every material movement transaction is recorded for audit purposes.
o Inventory condition and value can also be recorded.
o Barcoded items can be registered in the MMIS inventory system and IUID labels can be created in various formats.
o As material is shipped between sites and locations, shipping and receiving documents can be created for audit purposes and applicable shipping documents such as DD1949s or DD1348s can be created.
• Inventory Analysis
o Inventory criticality and lead time can be stored and if required, economic order quantity analysis can be performed for each inventoried item.
o Reorder points and minimum stock levels can be monitored, and rolling-through-time calculations can be performed if demand metrics are available.
o Failure rates and mean time between failure data can also be associated to each inventoried item.
• Maintenance
o Scheduled (PMCS) and unscheduled maintenance can be strategically planned and executed using the MMIS Workflow system.
o Preventive maintenance schedules can be created and applied to applicable inventory based on various triggers such as calendar days, operation hours, or other customizable measurement bases.
o Maintenance performed by field service representatives can be monitored and requests for spare parts can be easily dispatched.
• Workflow
o Standard workflow operations (or routes) can be assigned to parts that enter the depot for repair.
o Condition code and status can be recorded for each WIP item and metrics such as Repair Turn-Around Time (RTAT), Operational Availability, and Mean Time Between Failures (MTBF) can be calculated.
o Standard performance metrics such as touch labour estimates can be recorded and compared with actual labour hours and applicable support equipment, required conditions and consumables can be attached to each maintenance task that is performed.
o Work instructions can be created and attached to operations in MMIS for reference.
o Documentation such as shipping and receiving forms, maintenance actions forms, certificates of conformance, and failure data can be attached to each work order for future reference.
• Remove and Replace Procedures
o Every remove and replace procedure can be logged for future reference. Defective component and root cause analysis can be performed on repaired items as they move through the depot. This information can be synthesized use by reliability engineers for FRACAS reporting.
o If defect trends are identified engineering changes, training requirements or process changes can be presented to all stakeholders via a Failure Review Board or similar processes. If engineering change orders are created, MMIS can manage the incorporation of those changes.
o Inventory can be tracked geographically to the site/location/shelf and bin level and every material movement transaction is recorded for audit purposes.
o Inventory condition and value can also be recorded.
o Barcoded items can be registered in the MMIS inventory system and IUID labels can be created in various formats.
o As material is shipped between sites and locations, shipping and receiving documents can be created for audit purposes and applicable shipping documents such as DD1949s or DD1348s can be created.
o Inventory criticality and lead time can be stored and if required, economic order quantity analysis can be performed for each inventoried item.
o Reorder points and minimum stock levels can be monitored, and rolling-through-time calculations can be performed if demand metrics are available.
o Failure rates and mean time between failure data can also be associated to each inventoried item.
o Scheduled (PMCS) and unscheduled maintenance can be strategically planned and executed using the MMIS Workflow system.
o Preventive maintenance schedules can be created and applied to applicable inventory based on various triggers such as calendar days, operation hours, or other customizable measurement bases.
o Maintenance performed by field service representatives can be monitored and requests for spare parts can be easily dispatched.
o Standard workflow operations (or routes) can be assigned to parts that enter the depot for repair.
o Condition code and status can be recorded for each WIP item and metrics such as Repair Turn-Around Time (RTAT), Operational Availability, and Mean Time Between Failures (MTBF) can be calculated.
o Standard performance metrics such as touch labour estimates can be recorded and compared with actual labour hours and applicable support equipment, required conditions and consumables can be attached to each maintenance task that is performed.
o Work instructions can be created and attached to operations in MMIS for reference.
o Documentation such as shipping and receiving forms, maintenance actions forms, certificates of conformance, and failure data can be attached to each work order for future reference.
o Every remove and replace procedure can be logged for future reference. Defective component and root cause analysis can be performed on repaired items as they move through the depot. This information can be synthesized use by reliability engineers for FRACAS reporting.
o If defect trends are identified engineering changes, training requirements or process changes can be presented to all stakeholders via a Failure Review Board or similar processes. If engineering change orders are created, MMIS can manage the incorporation of those changes.